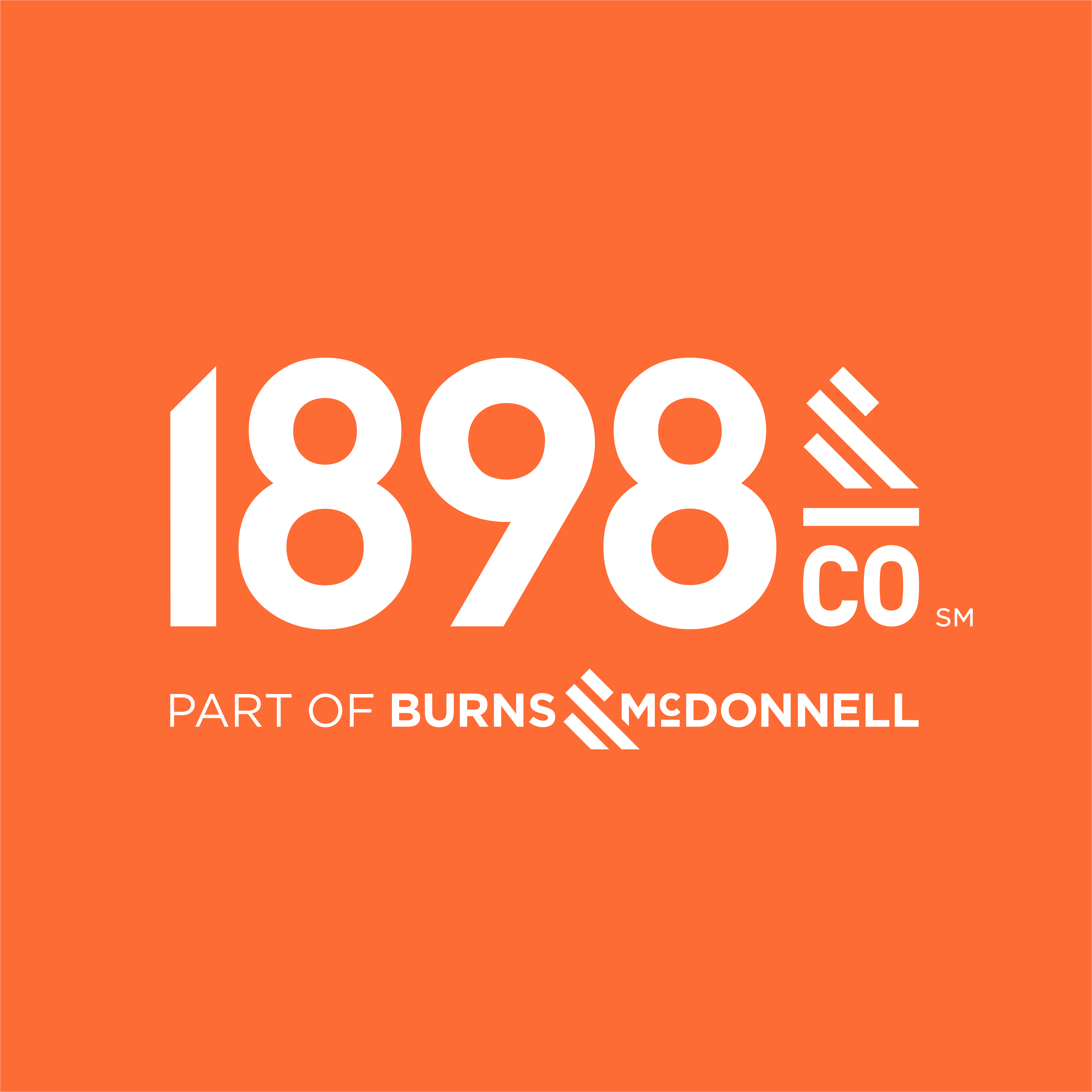
How and where we grow our food is changing radically. With the rise of the farm-to-table movement as well as an increase in the number of food recalls for various problems, more consumers are turning to local solutions for their food. These are changes that will have an impact on electricity use and grid design soon. Add cannabis legalization into the equation, and the country is now facing an almost nationwide agricultural transformation.
Agriculture in developed and some developing nations has been facing crucial change over the last decade. In traditional U.S. agriculture, produce travels an average of 1,400 miles from remote locations to urban centers. In Europe the distance is shorter but still significant. Shipping 1 ton of produce generates 0.25 ton of carbon dioxide (CO2) alone. Traditionally, seasons and weather have dictated the when, where and what of planting. Areas became known for what they grow. For instance, California is known for winter strawberries, and Mexico is known for winter salad ingredients. Greenhouses were introduced to the food production process to bypass some of the adverse seasonal effects, while still allowing for the use of sunlight.
The latest agricultural revolution has two main drivers: indoor agriculture and the state legalization of cannabis. This agriculture revolution will change what is consumed, how fresh it is, and how much energy is required for production. Electric utilities nationwide have already started investigating some of the effects of these changes to the power grid. An effort to continue quantifying these changes is needed both in the short and long term to help utilities better prepare for this load increase.